事業計画
plan
1. 本計画策定に至る背景
産業界(川下製造業者)からの要請
当社は、既存事業において溶接加工などを行っている。接合・実装に係る技術に関しては、接合部の高強度化、信頼性の向上や軽量化、接合・実装の位置精度の向上が求められており、接合部の機能の高付加価値化、信頼性の付与が急務となっている。
以下にあげる項目が、取引先である豊田自動織機(川下製造業者)などから求められているものである。
(ア)高強度化
耐久性の向上及び軽量化、コスト削減と調和する部材の高強度化は、様々な川下製造業者等で課題・ニーズとして顕在化している。
(イ)軽量化
様々な機械装置は一様に軽量化が進む傾向にある。大量の部品が使用されている輸送機械等では、接合用部品にも強度を維持した上での軽量化が求められている。
(ウ)製品の信頼性
接合部の緩みは構造物・電子装置の深刻な事故の原因となることが少なくない。日本製品に対する高い信頼性を今後も維持していくためには、製品の接合部の強度設計と緩み機構、さらにその防止設計の技術を高めるとともに、接合部の品質とメンテナンス性の向上に努めることが重要である。
(エ)環境負荷の低減
製造業に課せられる環境への責任は年々強まりを見せている。このため省エネルギー、低環境負荷、リサイクルに配慮した設計を行う等、環境負荷の低減は重要な課題となっている。
(オ)生産性の向上
新興国のメーカーはコスト競争力に優れ世界的に市場を拡大している。労働コストが高い我が国の製造業が競争力を維持し続けていくためには、限られた労働力で高い付加価値を生み出していく仕組みを構築することが不可欠である。
(カ)低コスト化
新興国等の競争が激化しており、品質・機能だけでなく、更なる低コスト化が求められている。
現状
下記のような問題がある。
コスト
溶接
溶接は手作業ではなく溶接装置を使用して実施するが、それでも部材の設置や機械の設定等、多くの人手を必要とし、コスト負担は大きい
検査
信頼性を確保するために全数水没検査を実施しており、検査については目視せねばならず、やはり多くの人手を必要とする。
歩留まり
検査の結果の歩留まりも90%程度で、やはりコストの問題が大きい。
生産性
上記のように溶接・検査ともに時間がかかり、現在以上の生産性アップは難しい。生産量を増やすには、設備と人の増加に頼らざるを得ない。
これらの要請、問題点の解決のために、当社は・・・
フォークリフト等の油圧配管の接合部における特殊加工
を行う。
2. 本計画の具体的内容
本計画の概要
これまで、フォークリフト等の油圧配管他、金属パイプの接合部等の、配管とネジ部分のパイプ径が異なるものは溶接されていた。しかし、従来通り溶接しているようでは、前頁にあげたような高強度化・軽量化・生産性の向上といった要請に応えることはできない。
そこで、本計画において当社は、パイプとネジ部分を溶接するのではなく、パイプを貫通させ、ネジ部分をパイプの周囲に接合する特殊加工を行い、川下製造業(特に自動車メーカー等)からの要請に応える。
本計画のイメージ図
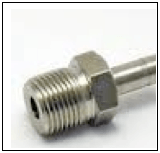
試験・評価
以下の項目について試験を実施する。
客先要求項目と評価方法、評価値
評価動画
1. 耐圧試験
定格圧力の4倍の圧力を加えて5分間保持して、漏れまたは破損がないこと。
注)定格圧力とは”連続できる最高圧力”とJISの油圧用語で定義されている。
ここでは20.5Mpa[209kgf/㎠]の値を示すこととする。
2. 耐衝撃圧力試験(JIS B2351-1977)
衝撃力のピークは定格圧力の150%±7%とし、周波数は30~75サイクル/minとする。
合計20万衝撃サイクル試験を行い漏れまたは破損がないこと。
3.耐振試験(JIS B2351-1977)
表1に示す曲げ応力が管の固定端に生じるような繰り返し荷重を1400サイクル/min以上の割合で加え、同時に定格圧力を加えて100万振動サイクルに達するまでに、漏れその他の異常がないこと。
管の外径(mm) | 6.4 | 9.5 | 12.7 | 15.9 | 19.1 | 25.4 |
---|---|---|---|---|---|---|
曲げ応力(N/㎟{kgf/㎟}) | 98{10} | 98{10} | 98{10} | 78{8} | 59{6} | 39{4} |
© 新郊パイプ工業株式会社